Movement in New Spaces of Logistics

Claire Haugh / 2018
Yale School of Architecture
“The traditional focus on physical materials, goods, and on information as the primary flow objects has already started to be expanded to financial and value flows, to flows of ideas, energy, and knowledge.” (Klaus/Muller, The Roots of Logistics, 20)
The discussion of logistics is centered around the ‘flow’ of goods and services, but much less on the flows of the people and technologies that enable these products and processes. If close analysis of material flows provides the ability to optimise logistical systems, what is the value of exploring the productive flows that occur when these products are made?
“At one point, one of the arms knocked over a tote, sending a dozen or so cone-shaped plastic coffee filters skidding across the ground. Scott hit a button that froze the arm so she could safely pick up the mess. Then the arms started working again. “The robot will work the same all day long,” said Edward Cohoon, who supervises Scott and other Amazon workers as they tend to individual robots. “Their stomachs don’t grumble.” (Wingfield, “Amazon Brings in the Robots, Forcing Humans to Find New Roles.”)
Collaborative robots, or cobots as they have recently been nicknamed, are being developed to drive new forms of manufacture in the logistics industry. Whilst isolated automation is still ruling supreme within this field, autonomous machines and technology often require a human counterpart to teach and guide their working processes. This collaborative work takes many forms, some more present in our global media, like those of Amazon’s KIVA warehouse robots, and others less known, like the Second Hands robots of Ocado Technologies and the cobots of FANUC Technologies and ABB.
Within these systems movement between robot and human becomes one of the predominant means of communication, efficiency and success. This booklet aims to explore these particularities of motion within this field, what happens to the movement of the human body when it becomes part of the logistical system? How does the embodiment of parameters and quantifications change the way a human worker might fit within this landscape and in turn, how does the necessity for robots to inherit human motion change the way we might view the technologies of logistical production?
Throughout the evolution of logistics, the analysis of motion has become a way to begin visualizing the intangible processes of production and in turn master its capacity for optimum efficiency. The spaces and architectures that have housed these processes have historically been shaped as a result of the evolving trends in motion and time optimization. If logistical architecture is designed around the movement of things then exploring the expanding movements of humans and cobots could give insight into new potentials in the architecture of logistics.
I plan to explore these ideas initially retracing of the history of human and machine production and the shifting shapes in movement of both of these ‘producers’. This background will be reinforced through an analysis into the simultaneous movement/spatial studies that have shaped movement in the logistical workplace and the processes of manufacture themselves. The relevance of these studies and their impact upon the field of logisitics has expanded to influence the new generation of cobots today. What are the new forms of movement that occur within this system and how do the human and robot begin to embody one another?
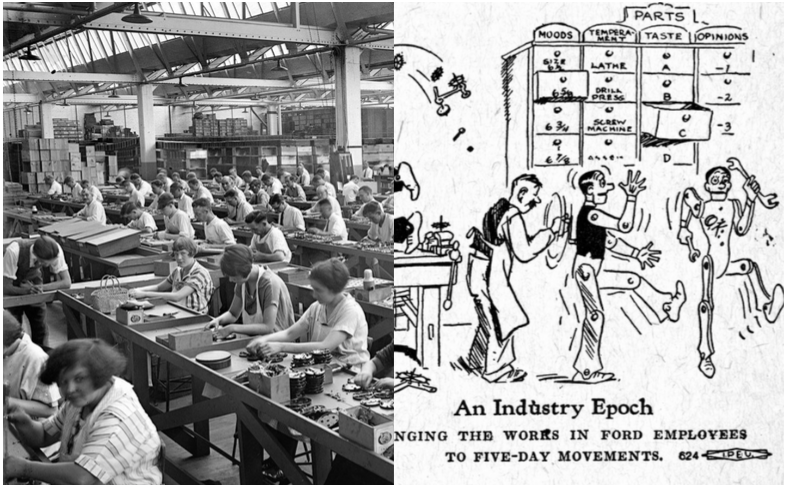
Theories of Work and Automation: Fordism, Taylorism, Post-Fordism, and Ergonomics
Spaces of manufacture had their origins in craft production where the worker utilized their skills and knowledge to produce singular and unique products. This involved very little physical engagement with machines, however tools became extensions of the human body. Motion was unique, unspecific and unregulated, it was not until the introduction of scientific analysis of time and motion that the overlaps between human and machine movement began to expand.
The first major shift in work culture came when Frederick Winslow Taylor brought the analysis of time and Frank and Lillian Gilbreth brought the analysis of motion, to the processes of production. The quantification of tasks and movement saw workers treated as modes of production not necessitating any distinctive skills but instead valuable in their ability to mimic the most efficient working patterns established by the studies. The floor of a Taylorist manufacturing space separated strategy from action (Business Dictionary). Movement became universally repetitive and was no longer individual but systematized through the optimisation of time. Where once a worker’s movements would vary around their own abilities and/or strengths at any given moment, their movements became fragmented and repetitive, more machine like in their quality, to maximise their productive abilities within the collective manufacturing process.
The implementation of the Taylorist methods meant that motions no longer varied as workers no longer Fordism, Taylorism, Post-Fordism + Ergonomics Theories of Work and Automation made products in their entirety, instead making just small component parts repetitively. Workers lost the autonomy of their own bodies and diversion from the universal movement was deemed to be an error in the logistical process.
Henry Ford’s production method known as Fordism, followed and expanded upon the key principles set in place by Taylorism, both of which had propelled the world of craft production into mass production. In this realm individual movement became collectively streamlined. The mechanism of a conveyor belt was introduced to allow the product being manufactured to move between workers gradually growing as each individual’s component was added. Each worker’s motion had a domino effect to the next and this was known as the assembly line, where time became optimised through the streamlining of movement. The assembly line typology became visible in the architecture of production during this period, most notably in the Ford River Rouge Complex which, perhaps for the first time, truly made visible the processes of mass production.
The apparent visibility or digestibility of the manufacturing processes involving machines and workers was soon blurred by the world of information technology whose influence arrived during the 1950s and 60s. Logistical production was no longer seen as only a force of material movement but now a power of service and economic flows that generated new economies in the shifting race for global dominance. This was particularly prominent for the relationship between human worker and machine technology, where for the first time, machines began to learn from the motions of their interactions with people. Where once analysis of motion and time was predicated on human optimisation, it was now the turn of technology. Movement of the human, in some ways, shifted back to the craft production era where each worker became autonomous with their tools and tasks were undertaken in their entirety. However the individual still moved within the constraints of pre-determined operational requirements of each machine, and so like Taylorism and Fordism before it, the space of post-fordism appeared as the space of repetitive non deviant motion. Now more than ever before, motion didn’t evolve the body but only the hands to operate the mouse and keyboard of computer systems.
The body did play a role however in the design of these machines and therefore their relationship to the worker as the field of ergonomics gained ground. Ergonomics saw design begin to play a major role in helping to facilitate the efficient movements of workers in relationship to the technologies and spaces of production that they were engaging with. This was also a major step in moves to begin representing human movement in the production workplace in a universally comprehensive manner.
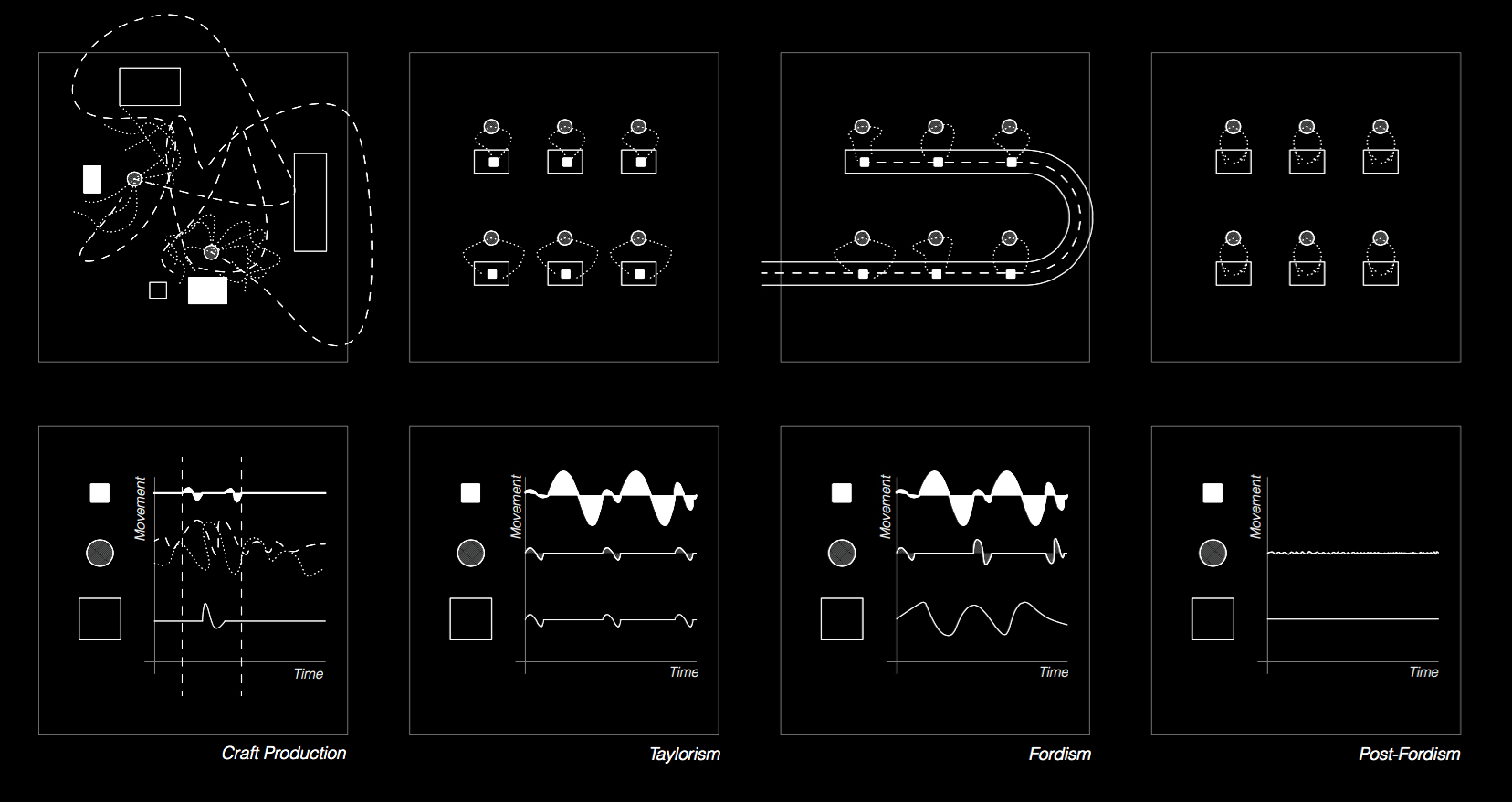
Movement and Representation
Time and Motion Studies:
Frederick Taylor’s time studies weren’t represented in graphic or pictorial form but instead, through quantifiable measurements of time and corresponding conversations with factory managers. So when Frank and Lillian Gilbreth generated their stop motion photographs it was one for the first times that this body of work exploring time and motion became visibly digestible. Recording the movements of workers in various manufacturing roles helped them to reveal the ‘unnecessary movements’ that were taking place in the field and reducing worker efficiency.
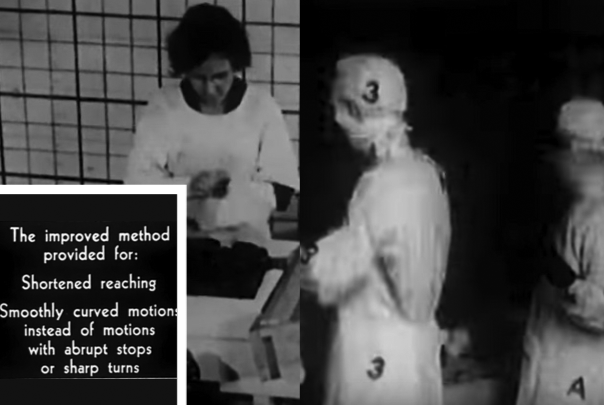
In these films the couple “break a workers every action into the smallest units”(PBS,”American Photography”) as if made up of component parts, locating whichever ones need adjusting or fixing. In these early studies it was often raw material placement and positioning that enables an increased productivity through efficient motion, but as technology developed the machine acted as the infrastructural partner to each worker, passing them the product to be made in a way that allowed them to remain in fixed locations with little movement. In the case of soap production as filmed in Gilbreth’s study, careful placement of pre-prepared soap packets lessened the need for the worker to move around in search of the tools and parts they needed. “A packet which makes possible a one motion grasp.”(Society for the Advancement of Management, “Original Films of Frank B. Gilbreth”)
When applying the Gilbreth theories on motion to the role of the bricklayer there was a 200% increase in worker productivity through a reduction in worker motion and therefore fatigue. The process of providing the materials for each step is facilitated in these early films by a team of people acting as a sort of conveyor belt effectively passing the product to the worker, this human conveyor extends through space and arrives at the worker’s fixed location. The films show odd relationships within space where the imagined machine (the team of people replication the motions of a conveyor belt) becomes an extension of the motion of the person, it’s flow dictates the flow and movement of the worker.
In many ways these efficiency protocols limited the body movements of workers, but in the example of the dating card process we see efficiency increase from the one handed process to the two hands and foot process. Whilst motion is regulated and repetitive it isn’t necessarily limited to to minimum limb utilization.
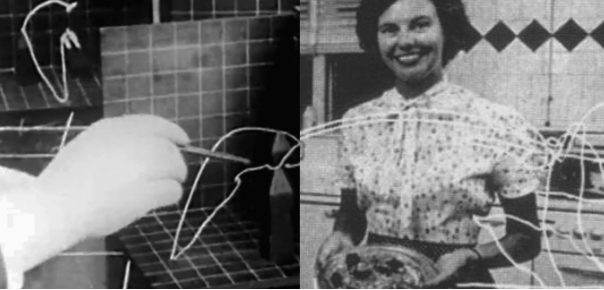
Physiogaphic Motion Studies:
In addition to these studies the Gilbreth’s produced a series of physiographic studies which involved small lights being fitted to the limbs of workers and then a slow speed photograph which traced the light and therefore the motion. These movements were re-spatialized through the production of wire models which gave a physical charting of the flows that each part of the utilized body would follow during the task at hand. When aligned next to one another the optimum motions could be determined by the length and path of its wire representation and by the timing that occurred during each photographic compilation.

Work Patterns + Ergonomics:
Using physical measurements of space in relation to the ergonomically defined human measurements, work patterns continued to be studied in the service industry. Now not only was the worker following the optimum motions of efficiency but technologies were being designed in a way that further facilitated their ability to do so.
New Spaces of Logistics: Relationships, Movements, and Manifestations
Amazon Kiva Robots:
“The robots, he explains, navigate the warehouse by pointing cameras at the floor that read two-di - mensional bar-coded stickers laid out by hand 1 meter from each other, in a grid. The robots relay the encoded information wirelessly to a computer cluster that functions both as a dispatcher and a traffic controller. It instructs, for instance, robot No. 1051 to bring rack No. 308 to worker No. 12—with - out colliding with robot No. 1433, which is crossing its path. To fulfill an order, a human operator stands at a pick-and-pack station on the perimeter of the warehouse. Robots crisscross the floor—they even use elevators to get to a mezzanine—and find specific racks to carry to the station. When the first robot positions itself in front of the worker, a laser pointer on a metal pole shines a red dot on a product. Once the worker has retrieved the item, the robot departs and another one takes its place.”(Guizzo, “Three Engineers, Hundreds of Robots, One Warehouse.”)

In contemporary spaces of logistics, like that of the Amazon fulfillment center, KIVA robots move easily, but for human workers through space is restricted and controlled. “The prime technique of power is now escape, slippage, elision and avoidance, the effective rejection of any territorial confinement with its cumbersome corralies of order-building, order-maintenance…” (Bauman,Liquid Modernity,9) In these “cavernous” territories the control of the human body has taken one step forward. Open and endless space once occupied by many hundreds of human workers, becomes physically inaccessible to anything but the machine.
FANUC , ABB, and KIT Collaborative Robots:
“Hello. We are FANUC’s growing family of CR (Collaborative Robot) Series robots! We’re the first-ever force limited Collaborative Robots from FANUC, and while you won’t find our picture next to the word “collaborate” in the dictionary (not yet, anyway), we were born out of the spirit of collaboration. We’re the first family of industrial robots of our kind - able to work alongside of your employees without the need for fencing, with the ability to lift and move objects from 4kg-35kg.” (FANUC,’Collaborate’)
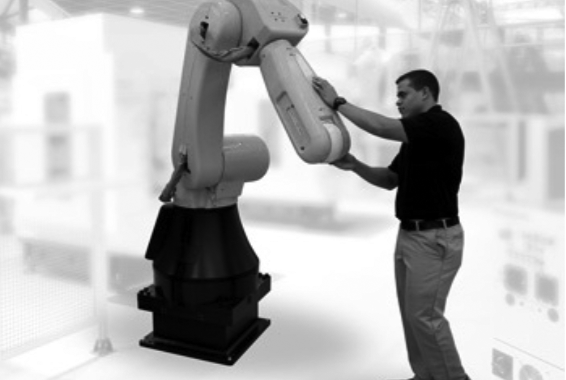
The FANUC, OCADO and ABB collaborative robots are expanding upon existing roles of cobots globally. Their work relies not on the distinct roles for human and bot interlocking with one another, but with the roles of each worker being influenced constantly by the other, particularly through sensibility to motion.
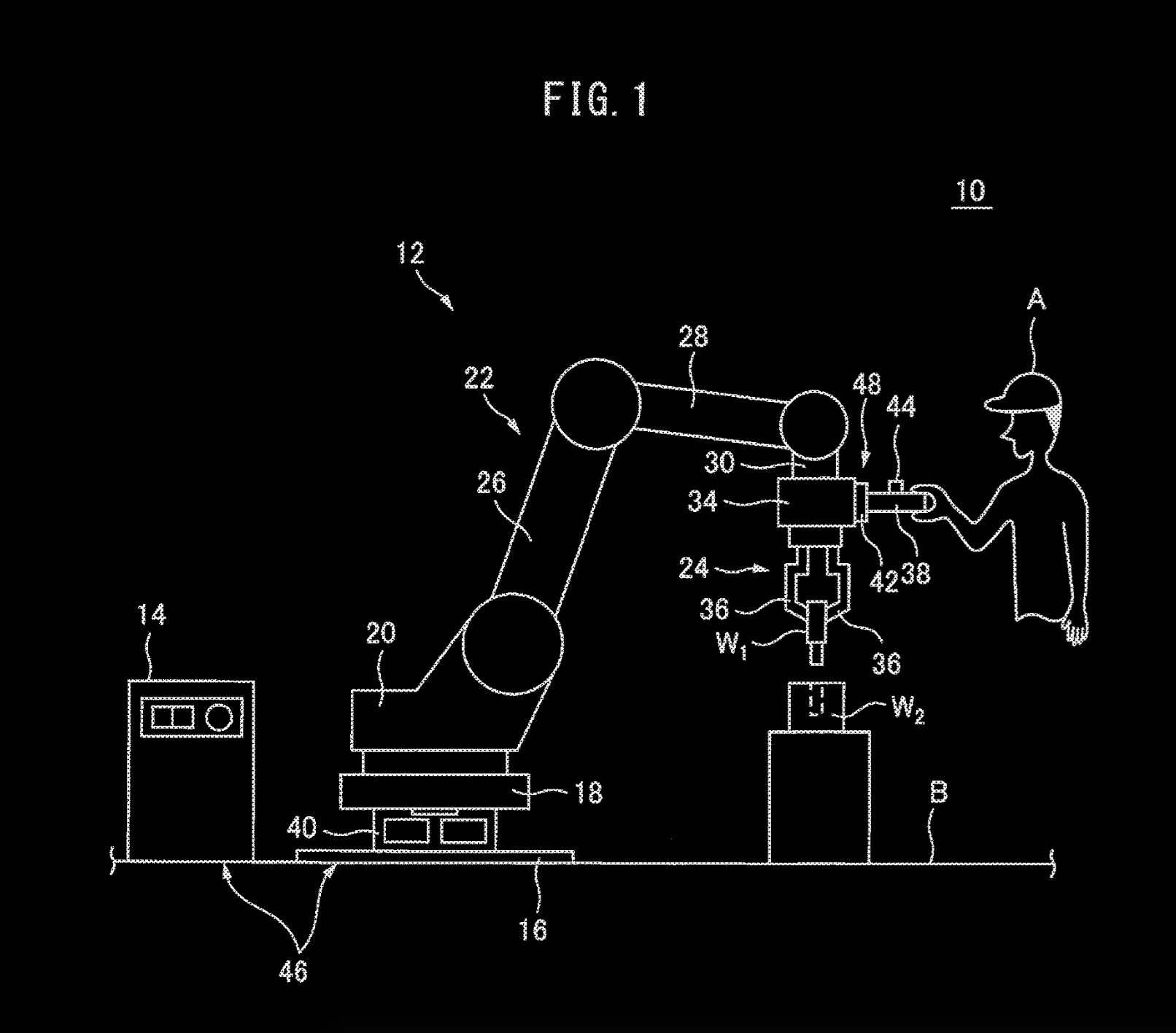
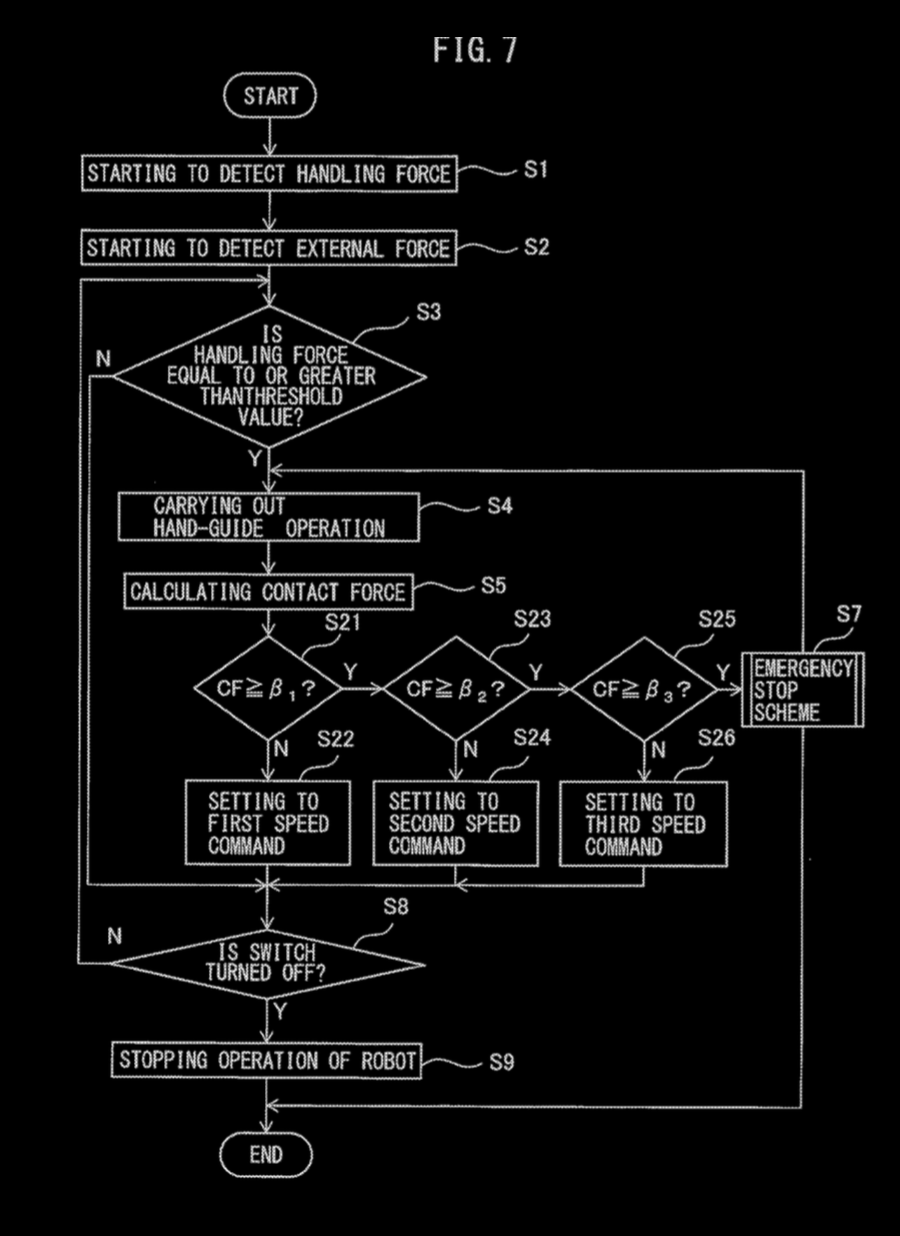
On the following pages a series of patent diagram and experimental film clips depict this unfolding collaborative space. Increasingly, as the images turn from construction based drawings to real-life mockups, the aesthetic clarity between robot and human begins to dissolve. Not only is this due to the particular design of these new technologies, but it is also due to the way that they have been designed to move in forms that closely replicate the human worker.
This replication and unification in motion and form take place within backdrops that could seemingly be ‘anywhere’, in UCL’s research movement experiments, the workers are placed in an easily recognisable warehouse environment and in another for KIT, the movement study occurs in what appears to be a laboratory.

Conclusion
The space of logistics has historically optimised the movement of goods, by restricting the movement of workers involved in the processes of production. Logistics has facilitated a “changing relationship between space and time” (Castells, The Rise of Network Society, 8) and it is particularly evident in the processes of manufacture and production, as explored in the motion studies within this booklet.
But as the logistical field expands into territories where human and robot collaborate these restrictions have become less visible. Through the analysis of the cobot and worker, a shifting dynamic is made visible where the movement of machine is more heavily influenced by that of the worker. In this realm the human relinquishes much of the autonomy that was lost with the introduction of Taylorism and its restrictions on the human body. Here the robot and human perform a logistical dance, where one moves in sync with the other in order to perform a perfectly choreographed process of production. The human worker takes on the repetition and order of efficient production but that process becomes humanized through the ability of the machine to respond to the independent motions of that person.
“By continuously embracing technologies, we relate ourselves to them as servomechanisms... to use them at all, serve these objects.” (McLuhan,Understanding Media-Gadget Lover)
Much of the contemporary perceived threat of logistics, automation and technological expansion is a result of generations of workers finding their motions restricted and altered in favor of their mechanical counterparts. In these scenarios the human is disempowered in favor of the machine and becomes subservient to them. Undeniably the dominance of automation will see workers fitting into a frictionless system but what collaborate robots indicate is that frictionless doesn’t always equate to homogeneity. The realm of the cobot is a truly logistical realm that understands that things are not absolute, nor do they start and stop but instead everything flows into everything else.
If movement in new spaces of logisitics is about a flexible movement between human and machine, the types of spaces that might house these processes could be seemingly endless. Like the remote working environments of our contemporary world, perhaps new spaces of manufacture won’t be boxlike and flexible, but might already exist as everyday architectures ready to be utilized for production.
Bibliography ↗